What is partial pressure in vacuum furnace?
- dayvette2022
- Mar 19, 2024
- 3 min read
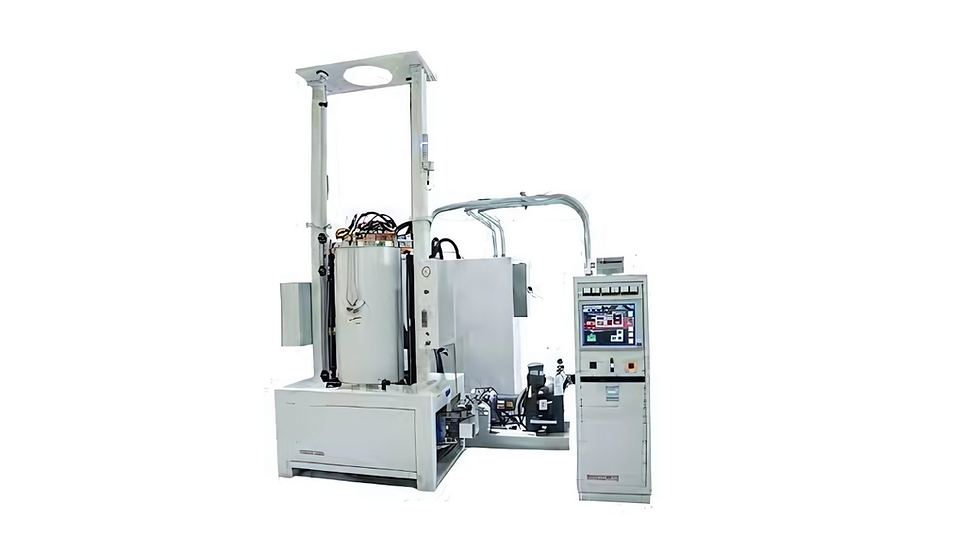
A vacuum furnace is a specialized type of furnace used in various industries for heat treatment processes under controlled atmospheric conditions. Understanding partial pressure within the vacuum furnace is crucial for optimizing heat treatment outcomes and ensuring the quality of treated materials.
Basics of Partial Pressure
Partial pressure refers to the pressure exerted by a single component of a gas mixture within a closed system. In the context of a vacuum furnace, partial pressure is essential for controlling the environment within the furnace chamber during heat treatment processes. It directly influences the rate and outcome of these processes.
Partial Pressure in Vacuum Furnace
Maintaining low pressure within the vacuum furnace is essential for several reasons. Firstly, it creates an oxygen-free environment, preventing oxidation of materials being treated. Additionally, low pressure helps in reducing impurities and contaminants in the furnace chamber, ensuring the integrity of the treated materials.
Control of partial pressures involves regulating the levels of different gases within the furnace chamber to achieve the desired atmosphere for specific heat treatment processes. For example, in processes requiring carburization, controlling the partial pressure of carbon-containing gases like methane or propane is critical.
The effects of partial pressure on heat treatment processes are significant. It influences the diffusion of atoms within the material, affecting properties such as hardness, strength, and microstructure. Moreover, partial pressure directly impacts the kinetics of chemical reactions occurring during heat treatment, ultimately determining the quality and uniformity of the treated materials.
Factors Influencing Partial Pressure
Several factors influence partial pressure within the vacuum furnace:
Type of gases present: The composition of the gas mixture within the furnace chamber, including inert gases like nitrogen and argon, as well as reactive gases like hydrogen and carbon-containing gases, significantly affects partial pressure.
Temperature of the furnace: Higher temperatures can lead to increased gas dissociation and higher partial pressures of reactive gases, impacting the kinetics of heat treatment processes.
Vacuum pump efficiency: The performance of the vacuum pump directly affects the level of vacuum achieved within the furnace chamber, thereby influencing partial pressure.
Monitoring and Measurement
Various techniques are employed for measuring partial pressure within the vacuum furnace, including mass spectrometry, residual gas analysis, and pressure transducers. Real-time monitoring of partial pressure is crucial for maintaining optimal process conditions and ensuring the quality of treated materials.
Applications and Industries
Vacuum furnaces find widespread applications across various industries:
Aerospace: Vacuum heat treatment processes are commonly used in aerospace applications for treating components like turbine blades and structural components to improve their mechanical properties and performance.
Automotive: Vacuum carburizing and nitriding processes are employed in the automotive industry to enhance the wear resistance and durability of transmission components, gears, and engine parts.
Semiconductor: Vacuum annealing and diffusion processes are critical in semiconductor manufacturing for optimizing the electrical properties and reliability of integrated circuits and semiconductor devices.
Challenges and Solutions
Several challenges are associated with maintaining optimal partial pressure within the vacuum furnace:
Leak detection and prevention: Ensuring the integrity of the furnace chamber and associated components is crucial for preventing gas leaks and maintaining the desired vacuum levels.
Maintaining stable conditions: Variations in temperature, gas composition, and vacuum levels can impact the consistency and quality of heat treatment processes. Implementing robust control systems and regular maintenance protocols can help mitigate these challenges.
Future Trends
Advancements in vacuum furnace technology are focused on improving process efficiency, reliability, and automation:
Advancements in vacuum pump technology: Developments in vacuum pump technology aim to enhance pumping speed, reliability, and energy efficiency, enabling faster evacuation and better control of partial pressures within the furnace chamber.
Integration with automation and control systems: Integration of vacuum furnaces with advanced automation and control systems facilitates real-time process monitoring, data analysis, and optimization, resulting in improved process repeatability and quality.
Are you ready to buy this product? It’s easy to purchase by visiting our product page!
Conclusion
Optimizing partial pressure within the vacuum furnace is essential for achieving desired heat treatment outcomes and ensuring the quality and reliability of treated materials. Understanding the fundamentals of partial pressure, its control, and its effects on heat treatment processes is crucial for maximizing the efficiency and effectiveness of vacuum furnace operations across various industries. By addressing challenges, leveraging advancements, and embracing future trends, the vacuum furnace industry continues to evolve, offering enhanced capabilities and opportunities for innovation in materials processing and manufacturing.
Comments